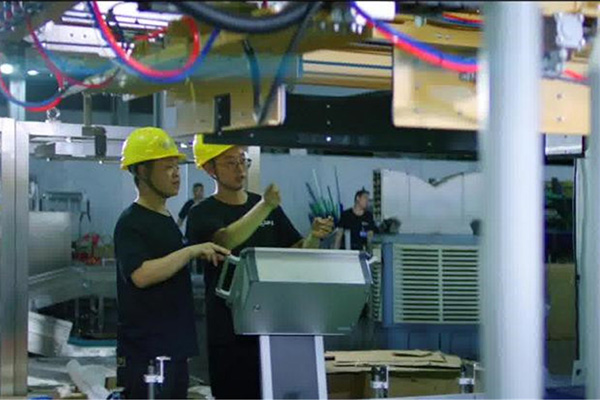
SAFE AND SUSTAINABLEP RODUCTION
PROVEN.RELIABLE ANDSUSTAINABLE PACKAGE SOLUTION
Product integrity and food safety
Cost effective and sustainable solution
20% reduction for installation time
Fast and safe commercial production
1. Q: What are the difficulties in non-standard automation design?
Answer: The plan. Only by understanding the product characteristics and processing technology can feasible and reliable implementation plans be proposed. Only under the guidance of the blueprint drawn by the designer can the project be implemented in an orderly manner and achieve the final effect.
2. Q: What is the most important aspect of non-standard automation design?
Answer: Nothing is unimportant. Every factor that affects the final acceptance is important, from the overall design scheme to the small screwwhich is not tightened.
3. Q: Which is better, dead positioning or adjustable mechanism?
Answer: Those who can do death positioning must resolutely do death positioning, and those who need to match positioning must match positioning; Concentrate errors, minimize adjustable mechanisms, avoid equipment debugging. Multiple adjustable components are matched with each other to achieve the final debugging effect, and the adjustment mechanism is finely tuned with a clear distinction between coarse and fine adjustments.
4. Q: What issues should be noted in mechanical design?
Answer: Positioning
1) The positioning of the processing object is related to the determination of the overall blueprint and solves the problem of customer needs;
2) The docking and positioning between single machines determine the reliability of connected production;
3) The positioning of components in single devices determines the compatibility between functional modules;
4) The positioning of parts in components determines the determinability of mechanism actions;
5) Clarify the concepts of positioning and locking, eliminate insufficient positioning, and avoid over positioning;
6) Positioning solves functional problems, and meeting functional requirements is a prerequisite for design;
Technics
1) Assemble technic. Whether the assembly process is feasible and easy to assemble and disassemble;
2) Structure technic. Whether it is convenient to process while meeting the accuracy requirements, and whether it is economical if it can be processed;
3) Process technic. Whether the process flow meets the requirements of part accuracy, strength, and lifespan;
4) The technic problem is about how to make;
Human-computer interaction
1) Is it convenient to operate, observe the operation of the equipment, and troubleshoot equipment malfunctions;
2) Is it convenient for equipment maintenance and repair;
3) Humanized design solves the problem of how to do better;
Breaking down the design of the assembly line step by step, and ultimately implementing the problem to every part and size, which makes the design less difficult.
5. Question: How do you view the issues of theory and practice?
Answer: Theory is the guiding principle for practice, and the failure to achieve theoretical results in practice is often due to the fact that the details in practice do not match the theory. Therefore, it is important to do every detail well; It is not denied that some theoretical foundations are not sound, leading to unexpected errors, so it is important to improve theoretical knowledge reserves; To achieve the best state of theoretical requirements, the final structure and theoretical effect will be almost the same. We should adhere to the correct theory as our belief and not easily negate it; After practical testing, if the gap between theory and practice is too large, one should dare to deny oneself and determine a new theoretical plan, after all, practice is the only criterion for testing theory.
Post time: Oct-11-2024